Thermal shock and thermal stress are the two main types of thermal failure in glass-lined equipment.
Shock
General thermal shock:
Any time your reactor experience a sudden change in temperature that is in excess to the recommended limit, you are exposing your vessel to potential thermal shock. Adding hot liquid to a cold vessel wall or conversely cold liquid to a hot glass surface creates an environment of increased tensile stress on the lining. This type of damage is usually so extensive that the entire vessel needs to be reglassed to repair it.
There is a simple solution to this though – just reference our handy “Maximum Allowable Thermal Shock – 3009 Glass” chart and you can easily determine the safe temperature differentials for 3009 glass lining. The chart is easy to read:
- The left side of the figure shows the acceptable temperature range of the jacket fluid based on the temperature of the product in the vessel. This data is needed when you are introducing a heating or cooling fluid into the jacket.
Example 1: If the glass-lined wall (and the batch) is at 356°F, the fluid introduction should be between 86° F and 518°F.
- The right side of the figure indicates the suitable temperature range of the product based on the current temperature of the jacket fluid. This data is needed when you are introducing product into the vessel.
Example 2: The reactor is to be charged when the glass-lined wall or fluid in the jacket is 302°F; therefore materials between 32°F and 482°F may be safely charged into the vessel.
Maximum Allowable Thermal Shock – 3009 Glass
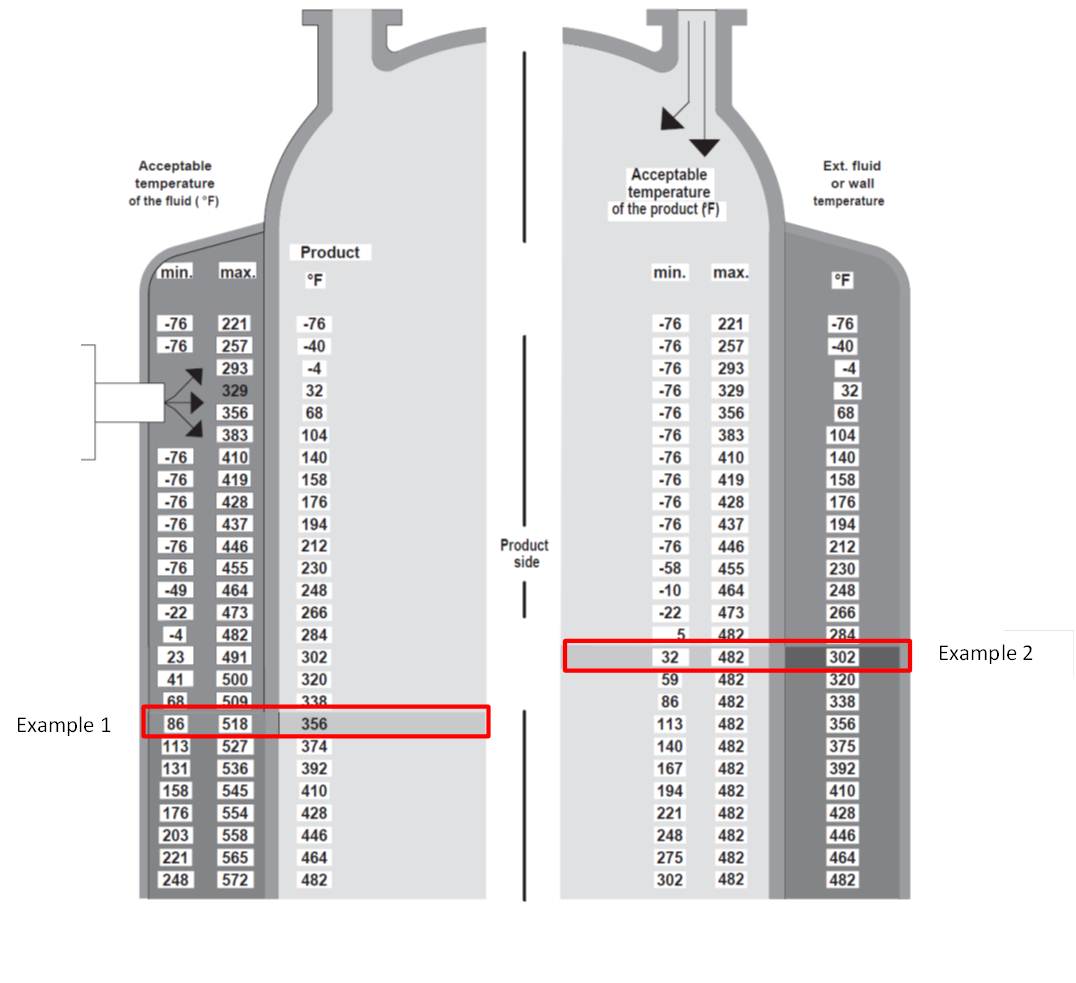
In general, the higher the operation temperature is, the lower the safe temperature differential. If you are ever unsure it is always best to consult with a professional who can give you the right guidelines.
Local thermal shock:
This term refers to thermal shock damage that is localized, for example, from a leaking valve that injects steam on a particular area of the glass-lined surface. Because the area is significantly smaller than general thermal shock which affects the entire vessel, a patch can sometimes be used as long as it can cover the entire damaged area.
Welding near glass:
One of the critical “don’ts” in glass-lined equipment care is “don’t weld components onto your equipment interior or exterior.” You should always contact your equipment vendor if any modifications need to be made to your vessel that would require welding. Welding and glass surfaces are generally are not a good combination due to the risk of thermal shock; welding on glass-lined equipment will almost always cause glass damage. Any major modifications can be made to the vessel during reglassing, such as changing the nozzle sizes, adding a nozzle, or adding supports. If you do attempt to weld on your own and cause damage to your vessel, the repair method depends on the size of the area and includes plugs, patches or even reglassing.
Stress
Restricted flexibility from large fillet welds:
Thermal shock is most prevalent at fillet welds between the vessel shell and jacket as well as at the top and bottom jacket closure rings. This is due to the high stress concentration in these areas. Additionally, any build-up of sludge in the reactor jacket and attribute to thermal stress risks. By blowing down the build-up on a regular basis, you can avoid plugging the outlet nozzle diaphragm ring which will decrease chances of thermal stress damage. Since this type of damage usually extends to the substrate, reglassing is most often the only viable repair option.
Expansion of steel:
The steel substrate of a vessel can expand for a number of reasons, freezing of the interior contents and over-pressurization of the vessel being the two most common. This expansion results in a series of cracks to the lining. In the case of agitators and baffles, if liquid that accumulates inside the hollow centers freezes, the glass often falls off in long shards. Expansion of steel damage is so severe that reglassing is the only solution; there are times when the steel is so badly deformed that the vessel is deemed unusable.