Guide to Selecting Filter Media for Nutsche Filter/Dryers
Nutsche Filter/Dryers are widely used throughout the chemical and pharmaceutical industries to separate a solid product from a solvent by using pressure/vacuum and agitation within a contained vessel, forcing liquid through the solid bed and filter media. When utilizing this technology in your process, it’s important to have not only a properly sized vessel (based on optimal cake depth), but the right filter media as well. This component is critical to the successful filtration of your product. In this post we’ll discuss the different options available and how to select which one will be right for your process (for a more high-level overview, read our post on Understanding the Nutsche Filtration and Drying Process).
Criteria for Consideration
Before reviewing the different media options available, you’ll want to take into consideration the following elements that will help you to determine what type of media is right for your application:
- Environment – In what type of setting will your equipment be installed? Environments can range from optimal (clean areas, labs) to hostile (mining underground, foundries).
- Component Sensitivity – How sensitive will the components be to contamination? Any potential sensitivities might lead you to select certain materials of construction over other options. Additionally, if your process requires cGMP, CIP, aseptic, and/or sterile design, those conditions often dictate the use of certain materials over others.
- Economic Liabilities – Do you have any budget constraints that need to be considered? The cost and frequency of component replacement need to be taken into account. Operational costs due to downtime, (i.e., delays in production) must be considered as well.
- Safety – Is your product hazardous or difficult to handle? It’s critical for operator well-being to have the proper safety measures in place as failure would cause severe damage to equipment or personnel.
- Life Expectancy – What is the service life required of the filter media? Depending on the corrosiveness of your product and production demands of your process, the life of filter media can range from a few hours to 20,000+ hours. Understanding the life expectancy requirements will help to predict downtime needed for filter media changeout.
- Pressure – How rigorous are your operating settings and duty cycle? Pressure setting can range from full vacuum, light/low pressure to severe/full pressure.
The Filter Base and Filtering Medium
The base of a nutsche filter dryer is comprised of a support structure (typically a perforated plate or solid heated plate) and filter medium. The type of support structure will depend on the requirements of the process. The heated filter plate provides heat energy directly into the cake from the underside, allowing for heat transfer through all of the filter contact surfaces, for more efficient drying. The perforated plate design allows for maximum open area for filtrate drainage or gas flow. Regardless of design, the base consists of a support plate strong enough to sufficiently hold the cake weight and pressure that is exerted on the cake's surface. All filter plate designs are capable of limited deflection when the unit is under full operating pressure.
The most common filter plate designs allow for the use of all types of commercially available sheet filter media. The three types of filter medium utilized with the nutsche most often include:
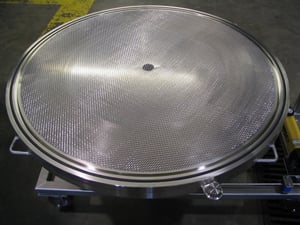
- Woven Wire Mesh Media – This media type is used for surface filtration and is available in a variety of weave patterns to suit the needs of the application. These could include plan square weave, dutch weave, twilled dutch weave, duplex weave, and many others. The varying weave patterns offer the ability to select a media for the specific needs of the process (mechanical strength, pore size, flow characteristics, etc.).
Pros:
- Easy to clean
- Mechanically robust to allow for less heel than cloth media
- Longer life cycle than cloth media
- Can be manufactured in a variety of materials to match equipment construction
Cons:
- Can be costly for exotic materials (Hastelloy)
- Less robust than sintered metal media
- Requires clamping hardware for installation (fasteners within the process area).
-
Synthetic Filter Cloth – Like woven wire mesh, this type of filtering media can be used for surface filtration, but it can also be configured in way to allow for depth filtration. Weave patterns can be designed with monofilament or multifilament construction and can be a single layer or multiple layered based on manufacturing techniques. In addition, textile media can include membrane technology for very fine particle retention. The varying designs offer the ability to select a media for the specific needs of the process (mechanical strength, pore size, flow characteristics, depth filtration, etc.) and offer great flexibility in process optimization.
Pros:
- Cheapest option
- Can be single use so that you do not have to worry about cleaning screen/cleaning product out of screen between batches and only cleaning the vessel
- Can offer very fine particle retention
- Can be provided in a variety of materials of construction to meet the needs of the process (nylon, polypropylene, polyethylene, PTFE, etc.).
Cons:
- Less durable than metal media
- Less robust than metal medias requiring greater agitator-to-media tolerance resulting in greater product heel
- Requires clamping hardware for installation (fasteners within the process area)
-
Sintered Metallic Plate – This type of media is manufactured using a sintering process to produce a rigid plate assembly that can perform filtration, but also has some structural capabilities due to material thickness. The material is usually manufactured using multiple layers of woven metal media sintered into a thick plate or by sintering metallic fibers into a porous solid plate. Both solutions can be manufactured in a variety of materials of construction (Hastelloy, stainless steel, and other exotic materials). In addition, the plate can be formed and welded to support extensive implementation as plate, tubes, cartridges and other forms.
Pros:
- Less heel than cloth media and single layer metal medias
- Last up to ~15 years
- Great for running multiple batches of same product
- Can be designed in a fully welded solution eliminating fasteners and hard to clean areas from the process area
Cons:
- Most expensive media
- Thickness of media can be difficult to clean for non-soluble products
- Can be difficult to handle for large installations
- Difficult to stock
Guidelines for Filter Medium Selection
The filter media selection depends entirely on the characteristics of the solids (particle size and shape, cake porosity, compressibility), cake thickness, the liquid and the appropriate materials of construction. Other guidelines to follow for filter medium selection include:
Filtration Rate
Nutsche filters function based on deep bed filtration principals. With deep bed filtration, the filter cake provides the primary mechanism for particle retention and resistance to flow. The filter media starts filter cake formation and as the process progresses the filter cake thickness increases. The filtration rate and efficiency become a function of the physical characteristics of the solids being retained and the parameters of the process (cake thickness, filtration pressure, etc.). The filter media will generally not impact the process rates. However, the media can negatively impact the process by allowing fines passage or plugging.
Testing
Due to the variety of products and parameters that effect deep bed filtration, it is critical to test products to determine media selection. Testing should be performed under conditions that closely mimic the process. The product should be representative of the material to be processed and the process parameters should match what is expected from the commercial process. This allows the media-to-product interaction to be simulated as close to real world conditions as possible. When testing it is important to understand filtration rate as a function of cake thickness and filtration pressure. In addition, observing solids bypass of the filter media or any types of media plugging is fundamental to a well optimized commercial filtration process. By testing various media types an optimal media can be selected that provides for good filtration rates, limited solids bypass, and reliable operation.
Testing for media selection can be performed using benchtop or pilot scale equipment. It is critical that testing be performed at the desired cake thickness and under pressure. Testing with thin cakes or only under vacuum is not recommended as performance can vary as the cake thickness changes.
Sizing
Filter medias are generally sized by porosity or particle retention. In determining the best size filter media for your process, it is important to know the particle size distribution of your product. This provides a starting point for media evaluation. Depending on your tolerance for fines or solids bypass, a media may be selected that is finer than the solids or that allows some fines passage during the start of filtration. With deep bed filtration, once the cake forms it will capture particles finer than the media retention rate. it is common for fines passage to occur at the start of filtration and to stop once a reasonable cake thickness has formed.
Since there is no theoretical way to determine filtration rate, suitable depth, or media selection, this information must be obtained via testing. De Dietrich Process Systems offers customers rental units supplied with filter medias of different materials and different porosity/micron ratings. We can also perform testing for customers in-house. If you need help selecting filter media for your application, you can reach out to DDPS for rental equipment and in house testing. We can support evaluation of media selection as well as process scale-up for all deep bed filtration applications.