Repair Materials and Techniques for Restoring Glass-Lined Steel
Glass-lined steel provides a tried and true, rugged design that has proven its value in countless applications across various industries that require a high level of corrosion resistance and durability in their process equipment. Nonetheless, people hear the term “glass” and often develop a negative perception of glass-lined steel, associating the material of construction with terms like “fragile”, “maintenance hassle”, and “costly”. But by familiarizing yourself with the unique properties and advantages of glass-lined steel you can dismiss these misconceptions. Additionally, by following the operating guidelines (specifically the temperature and pressure limitations) and performing routine vessel inspections and preventative maintenance services you can ensure your equipment will live a long, healthy life as well as optimize your process performance.
Even for the most meticulously run facility, there can come a time when minor to moderate glass-lining damage occurs - hopefully it’s not from a wrench falling out of your pocket as you entered the vessel (what were you thinking!). But fear not - there are several ways to get your equipment back up and running quickly. Once on the location and type of damage is assessed, the best repair material and method can then be selected. We’ve identified the most commonly used repair materials and outlined the various techniques used to restore the integrity of glass-lined equipment.
Repair Materials
Metals
Tantalum is the most common repair metal used in glass-lined equipment because its corrosion resistance is very similar to glass. When this level of corrosion resistance is not required (or inadequate in some instances) other metals are used, such as titanium, gold-platinum or even stainless steel. Some of these materials are less desirable because they are difficult to work with.
Cements
Furan, sodium silicate, and potassium silicate cements are often used in conjunction with other repair materials to fill in the spaces under the plugs, patches, or sleeves (these repair methods are discussed later in this article). They typically should not be used on their own, though in some instances sodium silicate cement can be used independently as a temporary repair. These cements all vary slightly in corrosion resistance and should be selected based on the credentials of the chemicals being used in the vessel. The cements consist of a two-part system that requires an accurate powder to liquid ratio, proper mixing, and precise working time to ensure it sets properly. It’s crucial when working with cement to carefully follow the curing times and temperatures to ensure an effective repair.
Epoxy Putty
Epoxy putties are comprised of various epoxy resins that contain nonmetallic or metallic fillers and are used similarly to cement repair materials. Additionally, epoxy putty is used to rebuild metal damage and help provide a level surface for gasket sealing. Epoxy putties are capable of withstanding this compressive stress and have proven to be useful internally for short-term repairs but are otherwise considered inferior to the resistance of furan and silicate type cements.
PTFE
PTFE gaskets are used to assist and support the metal repair. This material is also used in nozzle sleeves and as a sealing mechanism between the glass lining and the repair material. PTFE can withstand temperatures up to 500°F. In the rare instance that PTFE is not suitable for the process, PVDF or PFA can be substituted.
Repair Methods
Plugs
When a minor defect is found in a new vessel prior to factory shipment, or when there is a small area that was damaged by internal or external mechanical impact, a plug is most frequently used to repair it. The two types available are a one-piece plug which consists of a metal stud (usually tantalum) and a PTFE gasket and a three-piece plug (figure 1) that includes a tantalum disc and PTFE sealing gasket in addition to the former mentioned items. As mentioned before, cements are used in three-piece plug repairs to fill in the cavity of the damaged area and between the discs and the gaskets.
Figure 1
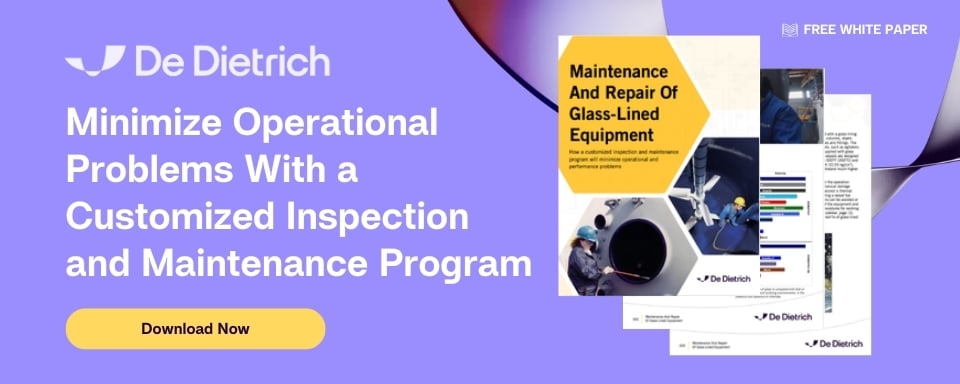
Patches
Patches become a necessary repair method when the size of the damaged area exceeds the coverage of plugs. Patches are most commonly made of tantalum and come in various shapes such as circles, squares or rectangles. Patches can be installed at the customer site in 1-2 days, minimizing downtime that is faced during more involved methods of repair like reglassing. Patches are comprised of a sheet of tantalum, tantalum studs and nuts, a sheet of PTFE, and repair cement (see figure 2).
Figure 2
Sleeves
Metal sleeves are most commonly used to repair damaged nozzles; the inaccessibility of this space due to the compact design of this vessel component usually prevents the use of a plug or patch in these small areas. There are three types of sleeves available – inside, outside and inside-outside. After evaluating the location of the damage and supplying the precise measurement, a vendor can supply you with the type of sleeve that will be the best fit. As with other repair methods, tantalum is the metal most frequently used in sleeve repairs. PTFE gaskets and cement are also used in conjunction with the metal sleeve.
Outside (figure 3) and inside-outside sleeves (figures 4a and 4b) constructed of PTFE can also be used to cover minor damage to the inside of nozzles. In the instance of inside-outside models, no cement, studs or nuts are required so installation can be achieved in only a few hours. However, it should be taken into account that the nozzle diameter will decrease by about one inch when this device is used.
Figure 3
Figure 4a (bottom outlet)
Figure 4b (top nozzle)
Repair Training
Glass-lined equipment repairs should only be performed by qualified personnel, usually the equipment manufacturer or an experienced contractor. Training programs are available to provide instruction and certification to enable in-house repair.
It is important to note that once a repair is made to the equipment it can never be considered permanent. Depending on service conditions, repair location, size, and quality of installation, the predicted life is variable. Best practices call for periodic inspection to monitor the condition of the repair to check for deterioration and loosening of the repair material.
Reglassing
Reglassing is the best solution when damage to the glass lining is moderate to severe and the addition of more plugs, patches or sleeves becomes uneconomical, or results in a repair of questionable integrity. Once your equipment is assessed to be a good candidate for reglassing based on the damage and condition of the steel substrate, it is shipped to the outsourced manufacturer and the reglassing process is performed at their glassing facility. At De Dietrich production plant in Corpus Christi, Texas, we can reglass all major brands of glass-lined steel equipment. During reglassing, many companies opt to upgrade their vessel with additional nozzles, OptiMix baffles, and insulation rings. The result is a “like-new” piece of equipment that features some “bells and whistles” not found on their original vessel.
Through inspection, testing and preventative maintenance, you can help protect your glass-lined equipment and extend its life for many years. When repairs do need to be made, as long as the proper repair methods are practiced and the right materials are used, you can continue to have durable, long-lasting equipment. We recommend consulting our free Glass-Lined Equipment Inspection eGuide as well as our Maintenance and Repair of Glass-Lined Equipment White Paper for additional information on glass-lined equipment.